Key points of this research results
- Mechanical behaviors are studied for cracked welded structures by physically based numerical simulation technique, i.e., extended finite element method (X-FEM).
- X-FEM fracture mechanics option of Code_Aster is utilized. Accurate simulation technique is examined by modifying the source code and script file.
- Fracture surface on brace/chord connection in a tubular joint is studied as shown in Fig. 1. Moreover, crack propagation simulation is carried out for a fillet welded joint including unwelded part in Fig. 2. New discussion based on fracture mechanics is succeeded to the fracture phenomena.
Outline
Structural damage sometimes occurs to welded joints due to several mechanical factors, e.g., stress concentration and welding residual stress. The welded structure and its structural members are very large and they have a complicated geometry. It is difficult not only for the damage detection but also for the maintenance and the crack extension prediction. Therefore, improvement of damage inspection technologies and residual life estimation to the welded structure is essential.
In addition to the experimental study, numerical simulation has been applied to investigate the fracture behaviors of the welded structures. A new structural analysis technique X-FEM has been proposed and gradually implemented to commercial/open-source software, e.g., Code_Aster. A basic study is carried out to enhance numerical accuracy of Code_Aster X-FEM option first. Then, the approach is applied to fracture behaviors of welded structures.
As shown in Fig. 1, fracture is occurred at chord/brace connection in a tubular joint. After the surface crack has penetrated to the chord surface, a twisted fracture surface can be seen in region A in Fig. 1. Numerical simulation is carried out to examine these fracture behaviors, and similar phenomena are obtained.
A fracture surface is observed for a fillet welded joint including unwelded part as shown in Fig. 2. The complicated fracture surface can be seen for presence of the unwelded part. Numerical simulation is performed to study the fracture phenomena. Branching and joining phenomena of crack front are exceptionally obtained employing the proposed approach.
For future study, several fracture behaviors will be analyzed employing such kind of technologies by the advanced fracture theory and numerical simulation methods.
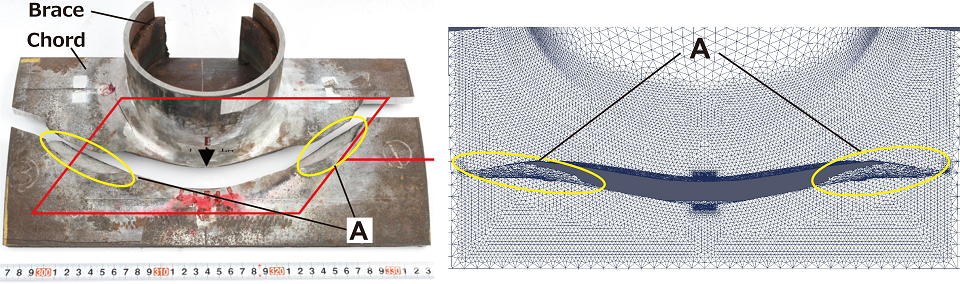
Fig. 1 Crack propagation simulation for a complicated fracture
surfacegenerated in connection of T-shape tubular joint
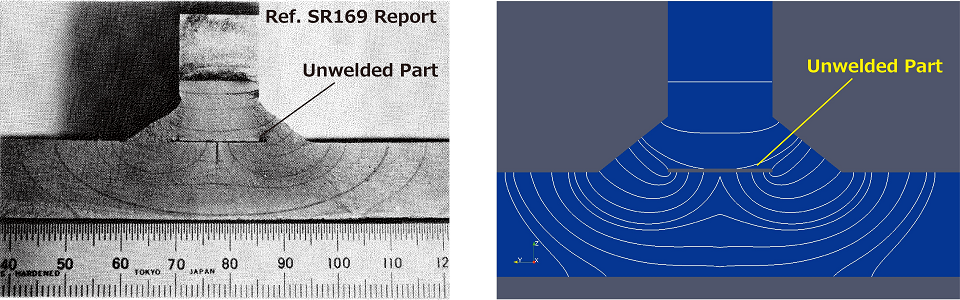
Fig. 2 Crack propagation simulation for a fillet welded joint including unwelded part
Paper Info
〇Journal Name:Journal of the Japan Society of Naval Architects and Ocean Engineers
Paper Title:Mechanical evaluation for a fatigue fracture surface generated in steel T-shaped tubular joints with different weld toe radius
(Vol. 32, pp. 141-152, 2020)
https://doi.org/10.2534/jjasnaoe.32.141
Authors:Kengo Maeda, Satoyuki Tanaka, Hiroki Takahashi, Kazuhisa Yagi, Naoki Osawa
〇Journal Name:Journal of the Japan Society of Naval Architects and Ocean Engineers
Paper Title:Investigation of crack propagation behaviors in a fillet welded joint employing X-FEM
(Vol. 33, pp.137-148, 2021)
https://doi.org/10.2534/jjasnaoe.33.137
Authors:Kengo Maeda, Satoyuki Tanaka, Hiroki Takahashi, Koki Tazoe
Reference Website for Code_Aster software: https://www.code-aster.org