Key points of this research results
- Dissimilar multi-material molding with high interface strength using hot-wire laser additive manufacturing (AM) technology has been successfully achieved for a dissimilar-material combination of stainless steel (SUS304) and aluminum alloy (A5183), which are difficult to directly bond and molding.
- If the stainless steel having good properties of a corrosion resistance and strength, and the aluminum alloy having good properties of heat dissipation and weight reduction, can be molded directly with a high interface strength, it will be possible to develop new products and components that utilize the characteristics of each material and greatly improve design freedom.
- Although this technology is still under development, it is expected to contribute to improving the performance of various products and reducing the environmental burden by applying it to various combinations of different materials and to various products.
Outline
The hot-wire laser AM technology being researched and developed at Hiroshima University combines the hot-wire method with a high-power diode laser to enable precise heat input control and a significant reduction in heat input to the substrate material, as well as ultra-high efficiency production. Mitsubishi Electric Corporation develops and sells wire laser metal 3D printers and is a top-runner in AM technology using lasers and wire supply. Joint research was initiated as there are many similarities in the content of the technologies both on both sides, and this achievement is one of collaborative research achievements.
In this study, the challenge is the direct molding of stainless steel (SUS304) and aluminum alloy (A5183), where the formation of very brittle intermetallic compounds (IMCs) is inevitable. Based on the innovative hot-wire laser AM technology, the effective use of fluxes effectively suppresses the formation of IMCs and enables high interface strength. Tensile test specimens were cut from the stainless steel (SUS304)/aluminum alloy (A5183) bonding interface of the fabricated objects to evaluate the interface strength, which was very high at 125 MPa on average.
To apply this technology to actual products, we plan to develop AM equipment and control technology in collaboration with Mitsubishi Electric Corporation. The technology can be applied to a wide range of metal materials other than stainless steel (SUS304) and aluminum alloy (A5183), and the development of a new additive manufacturing technology using a combination of different materials is planned. The results of this research have already been presented at domestic and international conferences. Information was also published in the Nihon Keizai Shimbun, Nikkan Kogyo Shimbun, Kobe Shimbun and other newspapers.
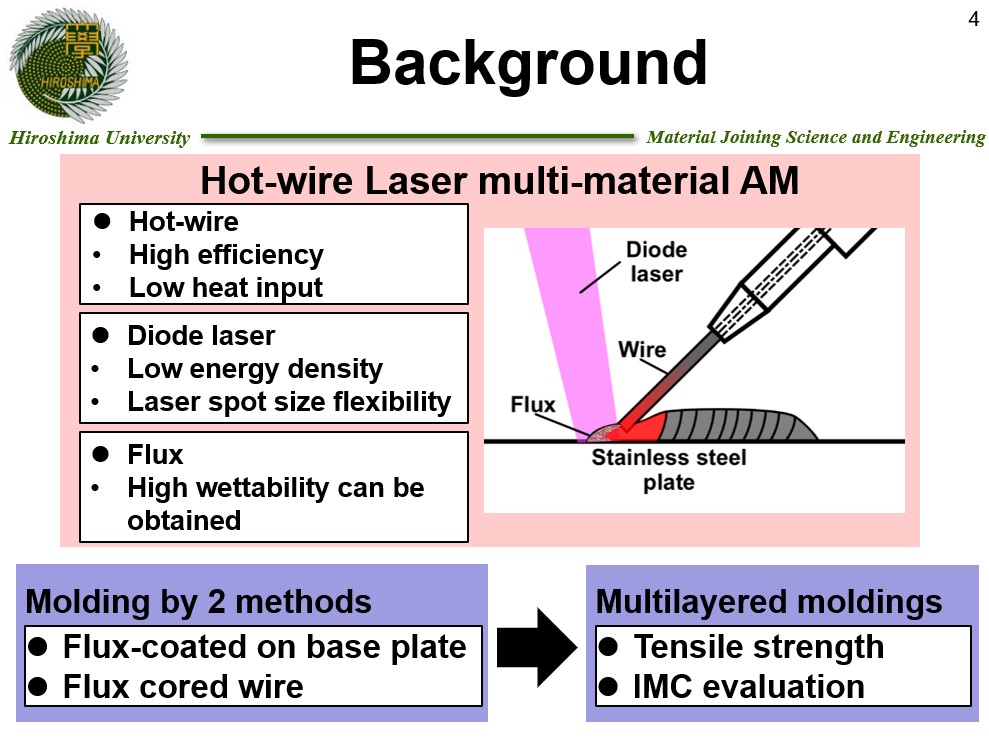
Fig.1 Features of multi-material AM technology based on hot-wire laser process.
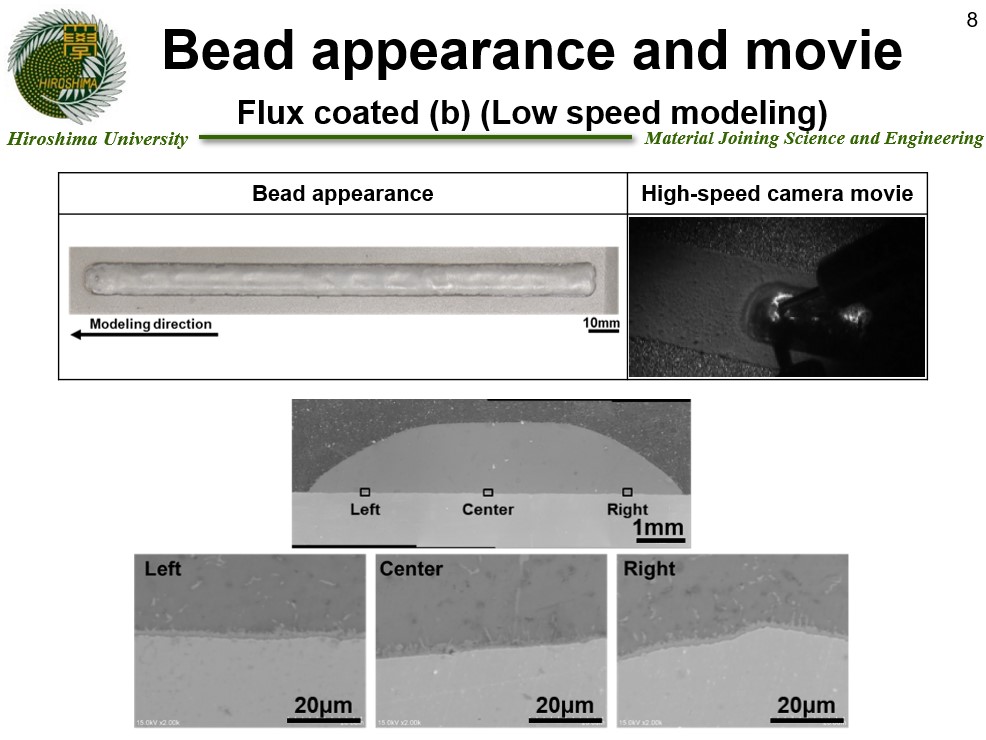
Fig.2 Aluminum alloy appearance molded on stainless steel plate, high-speed camera image during fabrication, SEM images on interface between SUS304 and A5183 (IMC formation).