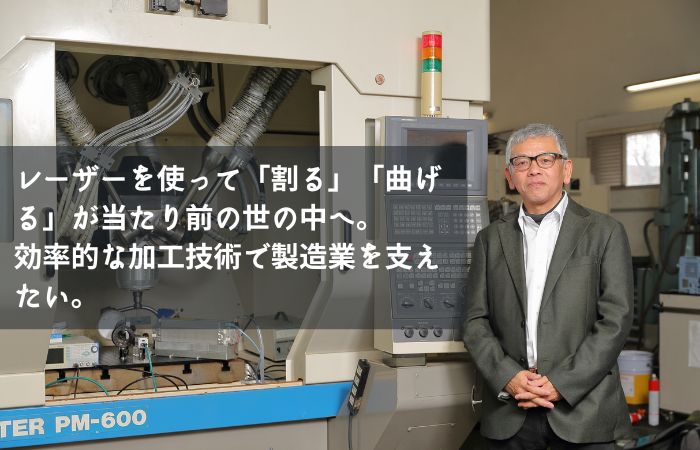
レーザーを利用して硬脆材を割ったり、金属材料の曲がり方を予測する研究
亀裂を走らせ「割る」加工で効率化・省力化に貢献
半導体の基板となるセラミックス、ガラス、シリコンなどの硬くて脆い素材(硬脆材)は、加工するために切削すると切屑が出ます。その切屑を出さずに加工するべく「切る」のではなく「割る」という手法に挑戦しているのが、私が研究するレーザー加工法です。方法としてはまず、材料のカットしたい箇所にレーザーを当てます。すると、当たった部分に周囲との温度差が生まれて亀裂が走り、材料が割れます。このとき、レーザーの照射部では材料が熱応力により膨張しているのですが、周囲の温度が低い部分は引っ張られて、ここに存在する亀裂が伸びていき、材料は切屑を
出さすことなく切断されます。精度よく切断するためには、不規則にならずに切りたい形に亀裂を生じさせることが必要です。
この加工法のメリットは、洗浄工程のないドライ加工であり、洗浄剤も使用しないので環境負荷低減にもつながること、また、材料の中を走る亀裂は理屈上音速に達する、従来の切断よりも時間短縮が図れることなどが挙げられます。もちろん、実際に音速近い速度で亀裂が進むと人間がコントロールできなくなってしまうため、レーザーを当てながらスピードも制御する必要があります。
実験では、硬脆材でできた1mm前後の厚みの板を使用しています。薄い板にレーザーを当てると、表面・裏面の温度差が小さいため比較的スムーズに板を割ることができます。しかし、板が分厚くなると温度差が大きくなってしまい、切断面が傾いたり、うねりが発生してしまいます。こうした課題を解決したり、将来的にはさらに硬い材料にも適応できるようにしていくことが現在の目標です。例えば、ダイヤモンドは半導体への利用が期待されている材料の一つですが、よく知られている様に非常に硬い材料なので、従来のように刃物を使った切断法では非常に時間がかかり、コスト高になってしまいます。「レーザーで割る」ことで精度高く切断できれば、ダイヤモンド製の半導体加工に有望だと言えるでしょう。他の応用先としてはガラスのディスプレイや、液晶ディスプレイ、スマートフォン用のガラスの切断などが考えられます。いずれも今は材料を「切る」ことが一般的ですが、「割る」ことが当たり前の世の中を目指しています。
未来の造船を支えるレーザーフォーミング加工
同時に研究を進めているものに、レーザーフォーミング加工というものがあります。先ほどご紹介したレーザー加工法と同じように温度が上がった際に生じる熱応力を利用しますが、今度は対象が金属材料に変わります。実用のイメージとしては、船の外板や自動車のボディーです。通常、自動車のボディーを大量生産する際は専用の金型を作成して金属の板を上下からプレスしていくのですが、金型を一つ作成するにも多額の費用がかかります。そこで、曲げたい金属板にレーザーを照射することで、金型レスで形成ができる
のではと考えました。この技術はプレス加工でできた形状を部分修正する際や、製品の試作をする際にも役立つはずです。
しかし、この加工法で板を2回、3回と曲げていくと、熱せられて膨張したり冷えて収縮した加工面がたわんでしまい、狙った形状に仕上げるために膨大なトライ&エラーを繰り返さなければならないとわかりました。そこで現在は、実験による加工結果をAIに学習させ、レーザーを当てた際の金属の形状を予想するという方向にシフトしました。この結果が安定して求められるようになれば、反対に、欲しい形状を入力する
ことでどこにレーザーを当てたら良いかが導き出せるはずです。特に造船分野は、現在も職人が片手にガスバーナー、もう片手に水の出るホースを持ち温めて冷やしてを繰り返しながら金属の形を変えるという工程をとっており、より良い加工方法を模索しています。レーザーだとガスバーナーと違い、狭い範囲でも限定的に加工できますし、エネルギーの調節もしやすく、扱いやすい技術になるのではと考えています。
将来のイメージが膨らむ社会実装に近い研究
私は学生時代から現在の分野で学んでおり、当時から研究職に就きたいと思っていました。理由は単純で、卒業研究がとても面白かったからです。当時はやることなすこと全てが新しいことで、金属の塊をゴリゴリ削って形状が作り出せること自体面白く、「この様に材料を加工して部品ができるんだ!」と感動していました。
研究で扱っている加工技術は製品製造に直接関わるため、社会課題への貢献を実感しやすいのも魅力だと感じています。実際に企業と共に進めているテーマもありますが、そう
した社会の要請に応えつつも、自分自身が楽しさを感じモチベーションになるような研究をすることも大切にしています。実験メインの研究をしているので、例えば今の時期なら、学生が仕上げた論文やその実験結果に目を通して起こったことを予測したり、なぜこうなったのか、どうすれば問題を解決できるのかと考えることも楽しみの一つです。
研究室には教員が3名、院生も含めて学生が20名ほど所属しています。実験棟には工作機械が並んでおりさながら町工場のようです。学生の就職先としては学んだことを直接社会で活かせるメーカーが多い印象です。研究の「出口」とでも言うべき社会実装に近い研究をしているため、機械製造業で働きたい人にとっては自分が社会で働く姿をイメージしやすいのではないかと感じています。また、工学部は学生数も多く、肌の合う仲間との出会いにも恵まれた環境だと思います。興味のある方はぜひ研究室にお越しください。
山田 啓司 教授
Keiji Yamada
機械加工システム研究室
1992年 3月 金沢大学 大学院工学研究科 精密工学専攻 修士課程修了 博士(工学)
1992年 4月 金沢大学 大学院工学研究科 助手
2002年11月 金沢大学 大学院工学研究科 講師
2005年 4月 広島大学 大学院工学研究科 助教授
2007年 4月 広島大学 大学院工学研究科 准教授
2015年 4月 広島大学 大学院工学研究科 教授
2020年 4月 広島大学 大学院先進理工系科学研究科 教授